Inside a sprawling PepsiCo manufacturing facility within the Netherlands that makes greater than one million luggage of potato chips every day, almost all of the plant’s greenhouse gasoline emissions come from a single step: frying the chips. The method has all the time run on a gasoline boiler. However the manufacturing facility will quickly activate a brand new system that may use renewable electrical energy as a substitute.
The tech, from a German startup known as Kraftblock, makes use of a delivery container full of small spheres designed to absorb warmth. When there’s lots of low-cost photo voltaic or wind energy obtainable on the grid, the system prices by utilizing the electrical energy to warmth up the fabric within the container. It will probably retailer warmth for a couple of minutes or so long as two weeks, releasing it on demand when a manufacturing facility wants it.
On the PepsiCo manufacturing facility, the modular new tech can be rolled out in phases. Within the first, the tech can lower emissions in half. Making the total change away from gasoline can in the end get rid of 98% of the plant’s emissions—as a lot as 17,000 tons of CO2 per yr.
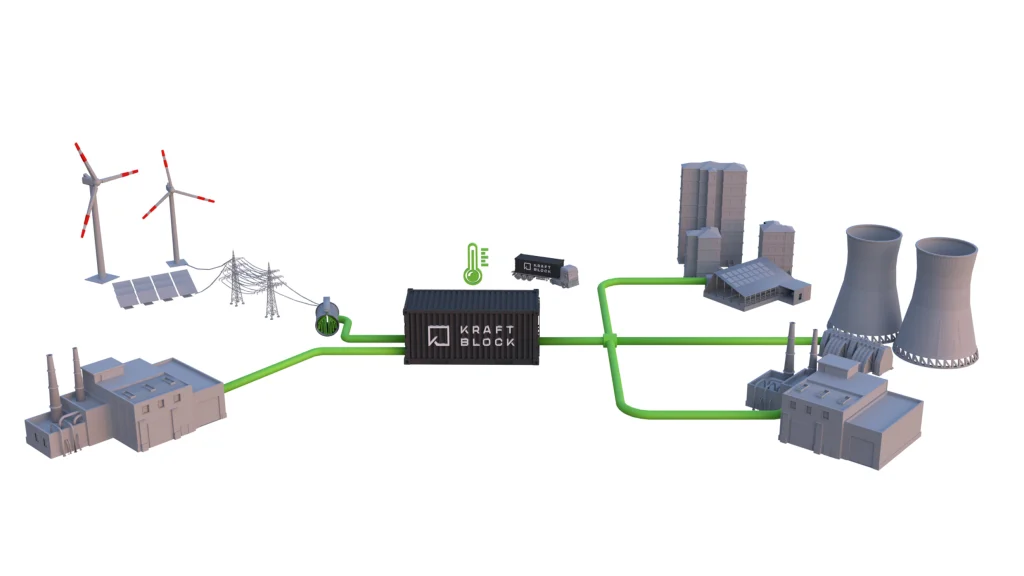
The identical tech can be utilized in any kind of manufacturing facility, from a metal mill to a brewery to a chemical plant. Industrial warmth is a significant local weather polluter, accounting for round 20% of world emissions. “For us, it was a no brainer to say, if we’re in a position to decarbonize warmth era, we are able to take an enormous step within the race in opposition to local weather change as a result of we might dramatically cut back carbon dioxide emissions,” says Kraftblock cofounder and CEO Martin Schichtel.
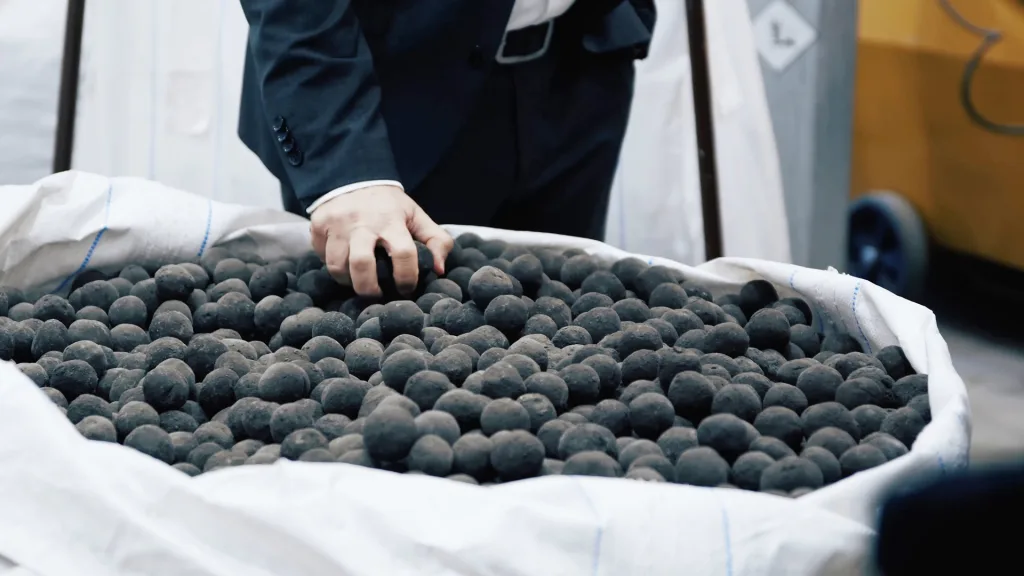
Up to now, it has been exhausting for producers to change to renewable power. Factories want a relentless supply of energy (the chip manufacturing facility runs 24/7, for instance) and photo voltaic and wind can be found intermittently. Factories are sometimes constructed round fossil-fuel-powered tools. And the extraordinarily excessive temperatures wanted for some industrial processes could be inefficient to run on electrical energy.
However Kraftblock’s tech can supply steady warmth, slot in with current tools, and supply warmth as much as 2,500 levels Fahrenheit. The working price is aggressive with operating on gasoline, Schichtel says. And factories can usually recuperate the price of the preliminary funding inside a few years.
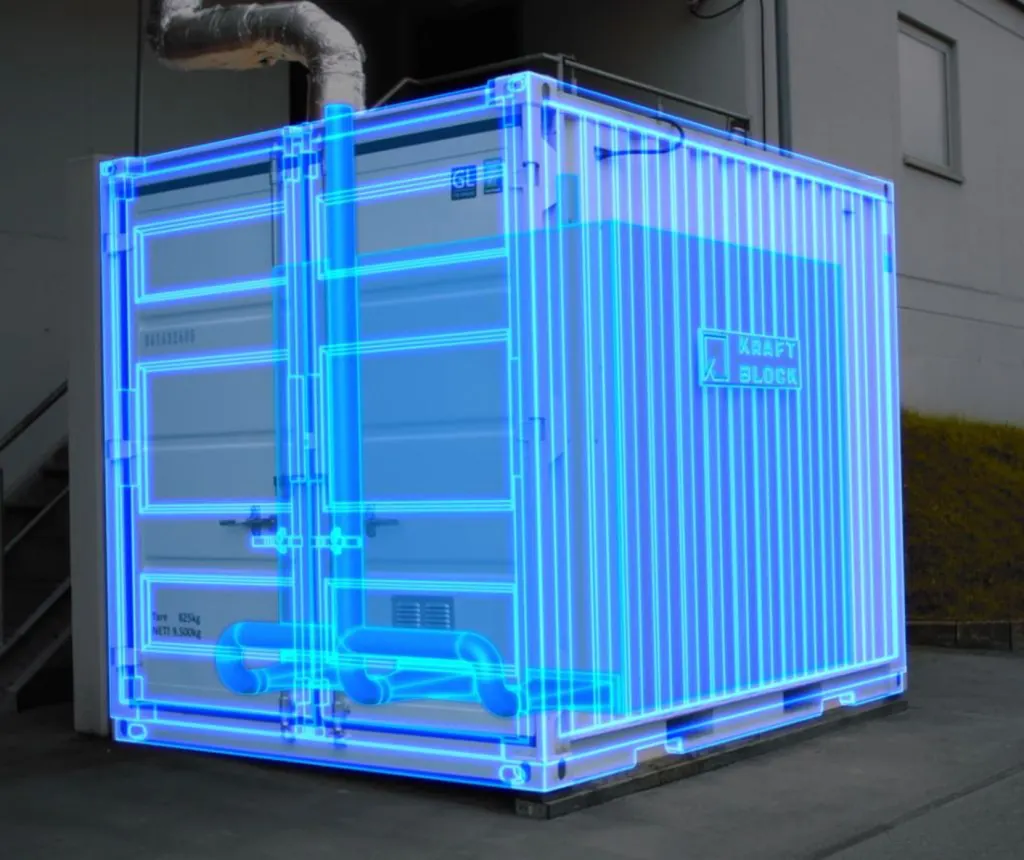
In one other challenge, the corporate is utilizing waste warmth from a ceramics manufacturing facility to recharge the power’s storage system. As a result of its know-how can present extra exact warmth than the gasoline system that the manufacturing facility beforehand used, the standard of the ceramics can also be enhancing—and the manufacturing facility has to throw out much less waste. Kraftblock is putting in methods in a number of different factories, together with a metal mill in India.
Startups like Antora Energy and Rondo Energy have developed comparable know-how, utilizing bigger “bricks” to retailer warmth. Kraftblock’s design is a bit of completely different, Schichtel says: The spherical form of its design offers extra floor space, so it could actually take in and launch warmth sooner. The “pellets” could be made in several sizes (on the Pepsi manufacturing facility, they’re a bit of smaller than golf balls) relying on how the manufacturing facility will use warmth. Every pellet is constituted of recycled supplies like metal slag which can be floor up right into a powder after which held along with a proprietary binder.
The corporate produces the tech in Germany, nevertheless it’s additionally starting to work with companions around the globe to license it and produce it themselves. “Which means we are able to scale fairly quick,” Schichtel says. The problem of shifting power sources is large: China alone has greater than 6 million producers.
Source link