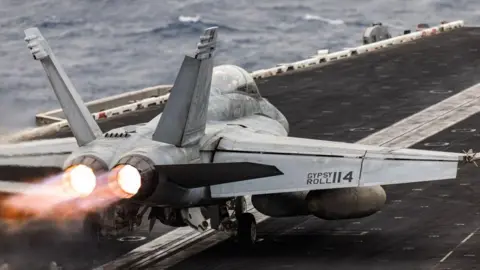
Jet engines are some of the jaw-dropping feats of engineering people have ever provide you with.
However jet engines shouldn’t be doable, says Ben Beake, director of supplies analysis at Micro Supplies, an tools testing firm in Wales.
“The air coming in is hotter than the melting level of the steel beneath – which is clearly not a great factor,” he explains, mentioning that this air reaches temperatures effectively above 1,000C.
Designers of jet engines have gotten round this downside by making use of heat-resistant ceramic coatings to the engine blades. And now, researchers are creating but stronger coatings that permit the engines to run hotter nonetheless.
“If you happen to get it to go hotter, then there’s a large saving on gas and CO2,” says Dr Beake. By growing the temperature by simply 30C or so, you may get an 8% gas saving, he estimates.
That is the ability of coatings – they radically remodel the performance and capabilities of an underlying materials. Few individuals realise how vital they’re, however these overlays and veneers can supercharge high-performance machines, or be certain that costly tools survives the harshest of environments.
Dr Beake and his colleagues are tasked with pushing coatings to their limits, so as to see how strong or efficient they are surely. His shoppers don’t all the time get the outcomes they need. He recollects telling a missile producer, “We’ve damaged your coating,” some years in the past. “They stormed off in a huff,” says Dr Beake.
In addition to exposing coatings to excessive temperatures, Micro Supplies additionally has a “woodpecker” machine, a tiny diamond stylus, which repeatedly faucets a coating at random places to check its sturdiness.
Lately, the agency has labored with UK-based Teer Coatings to check a product that could possibly be utilized to satellite tv for pc elements together with gears and bearings utilized in numerous shifting elements.
It’s a tough process, says Xiaoling Zhang, from the corporate, as a result of the coating should defend such elements each pre-launch (when they’re uncovered to atmospheric humidity at floor stage) and in addition in orbit, in opposition to mud particles and radiation in area. Nonetheless, she claims that the agency has achieved the specified outcomes.
However moreover defending spacecraft, coatings may additionally cease astronauts from getting sick.
Biofilms – gloopy accumulations of micro organism inside pipes – grow faster in low gravity environments, which could possibly be an issue for water provides or equipment that strikes fluid round on area stations or future spacecraft, for instance.
“Biofilms are identified to trigger mechanical failures,” says Kripa Varanasi on the Massachusetts Institute of Know-how. “You don’t need this.”
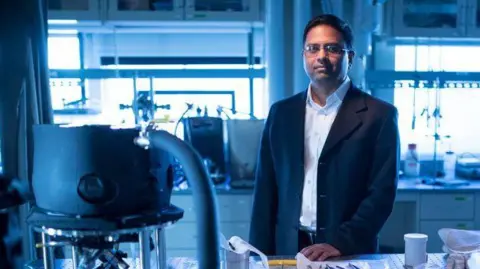
Prof Varanasi and his colleagues have developed a spread of coatings that make surfaces slippery and due to this fact immune to the formation of biofilms. Assessments of 1 such coating in an experiment carried out on board the Worldwide House Station discovered that it worked as intended.
The thought behind the coating is to combine collectively a stable materials and a lubricant. That is then sprayed onto the inside of a pipe or tube, which makes that inside floor extraordinarily slippery.
Prof Varanasi has beforehand made headlines for creating related coatings for the insides of toothpaste packets – so you may get each final little bit of toothpaste out. He and his colleagues have commercialised the expertise by their spin-out firm LiquiGlide.
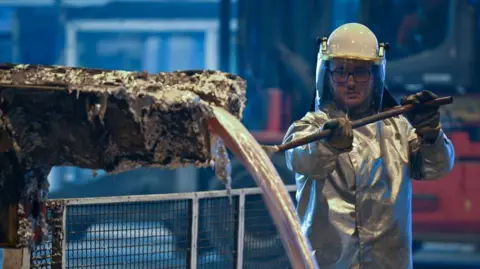
Slipperiness is, maybe, an underappreciated attribute. Nuria Espallargas on the Norwegian College of Science and Know-how and colleagues have developed a silicon carbide-based coating for tools utilized in aluminium manufacturing or restore.
It’s a type of non-stick frying pan resolution, which means that layers of molten aluminium don’t get caught on this costly tools. The exact functioning of this specific coating is at present one thing of a thriller, although.
“To be trustworthy, we actually don’t know the way it works, the mechanism is unknown in the mean time,” says Prof Espallargas.
Nonetheless, the coating is obtainable commercially by her spin-out firm Seram Coatings. Atlas Machine and Provide, a US agency that makes and repairs industrial equipment, has tried it out.
“The actual profit lies in extending the lifetime of the instruments and bettering the standard of the merchandise being produced,” says Jeremy Rydberg, chief innovation officer.
He says that, with out the coating, Atlas should rebuild the curler instruments it makes use of to work aluminium each two days. This prices $4.5m yearly. However the brand new coating implies that these instruments final for an entire week, not simply a few days, slashing these rebuild prices to round $1.3m per yr.

Coatings can do some superb issues, however they don’t all the time work as supposed, notes Andy Hopkinson, managing director at Safinah Group, a agency that usually will get referred to as in to research when coatings go unsuitable.
“We’re seeing a whole lot of points in the mean time with automotive parks, the place their passive fireplace safety system is peeling off,” he says, referring to the fire-resistant paint typically utilized to concrete constructions.
And his firm has additionally discovered that coatings utilized to industrial ships don’t all the time forestall barnacles and different sea life from attaching themselves to the hull. This downside, often called biofouling, will increase friction, which means the ship’s engine must work harder – and burn extra gas.
Regardless of the supply of coatings that promise to assist, ship homeowners don’t all the time select the proper one for his or her vessel. That alternative ought to rely upon the place the ship is crusing, how lengthy it is because of be idle relatively than in movement, and so forth, says Dr Hopkinson.
The price of fixing points like this could run into many hundreds, and even thousands and thousands of kilos. “Sometimes, paint prices between 1 and a couple of% of the mission. The issue is, when it goes unsuitable, the prices turn into exponential,” says Mr Hopkinson.
The researchers working on this discipline, although, say that there are nonetheless many alternatives to enhance coatings and develop new ones that would drastically enhance the efficiency of machines or infrastructure sooner or later.